Abstract
Incorporation of two dimensional (2D) materials into a polymer matrix is an efficient way to prepare high performance coatings. Here we report the in-situ mechanical exfoliation of graphite in a mixture of hydroxyethylacrylate terminated polybutadiene urethane (HTPU) prepolymer and reactive diluent. The mixture containing exfoliated graphite nanoplatelets (GN) is directly used to prepare UV cured composite resins (G/HTPU) with various GN concentrations. Various techniques, such as scanning electron microscopy (SEM), Raman, atomic force microscopy (AFM), have been used to characterize the GN, confirming that few-layered GN are obtained after the in-situ mechanical exfoliation. The incorporation of GN exerts little effect on the curing of the coatings with a gelation around 95%, but greatly enhances the elastic modulus. Tafel polarization curves, electrochemical impedance spectroscopy (EIS) and salt-spray testing were conducted to comparatively evaluate the G/HTPU coatings with different GN loadings. The results indicate that the incorporation of GN greatly improves the corrosion resistance of the HTPU UV coatings. The self-corrosion current density (I corr) and the charge transfer resistance (R c) of G/HTPU-2 (0.2% GN loading) are greatly reduced to 1.03 × 10-8 A·cm-2 and increased by two magnitudes, respectively, compared to those of the parent HTPU coating. Additionally, the G/HTPU-2 coating with thickness of 100 μm can protect galvanized sheet against 0.5 mol/l sulfuric acid for at least 24 h. The practical application in protection of electronics was illustrated by coating the G/HTPU-2 on a standard printed circuit board (PCB, IPC-B-24A). No corrosion was observed after it was immersed in an artificial sweat solution even under open-circuit voltage of 12 V for 72 h and then 24 V for 48 h.
Keywords
1. Introduction
Electronic products are becoming widely used in modern society, where a large amount of metal materials and electronic components are used. The electronic components are susceptible to corrosion due to chemical and electrochemical interactions with the surrounding environment during operation. Additionally, smart electronic devices, like cell phones, smart wristwatches, are going to feature higher integration, higher compactness, and so on, which face stricter protection requirements. Currently, the primary methods for preventing metal corrosion include coating protection[1], the addition of corrosion inhibitors[2], and electrochemical protection[3-5], etc. Among these protective methods, coating protection has been proven to be a facile and efficient method. Organic coatings, such as fluorinated resins[6], epoxy resins[7], polyurethane resins[8], and phenolic resins[9], are widely used as corrosion resistance materials, possessing the merits of good processibility, low cost and good corrosion resistance performance. Thermoplastic fluoroacrylate resins, which are dissolved in fluorosolvents, find wide applications in the anti-corrosion of electronic devices. The fluorous solution can be easily coated on substrates by various techniques, such as dip-coating, spraying, drop-coating etc. After the solvent evaporates, fluoroacrylate films form on the substrates. Ascribed to the good hydrophobicity, the fluoroacrylate coatings even with very thin thickness exhibit excellent corrosion resistance[10]. However, the fluorosolvents evaporation during the film forming process results in the environmental pollution and high costs. Recently, intense concern regarding the per- and polyfluoroalkyl substances (PFAS) has cast a shadow over the use of fluoropolymers.
UV-curable coatings, known for their efficiency, enabling properties, cost-effectiveness, energy savings, and environmental friendliness (5E), have wide applications in coatings, inks, adhesives and so on[11-14]. However, suffering from the surface oxygen inhibition and curing shrinkage, the UV-curable coatings cannot achieve very high cross-linkage. There is a continuous demand for improving the protective performance of the UV-curable coatings. It is well understood that the corrosion resistance of organic coatings relies on their ability to act as a barrier, effectively separating the corrosive medium from the metal surface. To intensify the barrier effect, materials with high aspect ratios such as graphene[15], boron nitride (BN)[16], are incorporated into the organic coatings[17-20], greatly improving the corrosion resistance performance. Dadkhah et al. successfully synthesized a nanocomposite comprising acrylated polyaniline/graphene oxide (PANI/GO) nanosheets. They employed this nanocomposite as a highly effective additive in UV-curable fluorinated polyurethane coatings[21]. Furthermore, they developed a UV-curable nanocomposite coating composed of fluorinated polyurethane acrylate and modified GO, showcasing exceptional corrosion resistance[22]. Jafarifard et al. presented a simple method for preparing a UV-curable coating based on GO. In the method, synthesized GO nanoplates were dispersed in epoxy acrylate (EA) UV-curable resin through a solvent-mediated dispersion, which reduced the shrinkage of UV-curable resin and improved the adhesion to substrates[23]. To improve the dispersibility of GO and its interaction with the polymer matrix, Ma et al. modified the GO using reactive PUA molecules and incorporated the modified GO into a polyurethane acrylate (PUA) UV-curable resin. The incorporation of GO nanosheets remarkably improved the corrosion resistance of the PUA matrix[24].
Exfoliation of graphite is a conventional method for the preparation of graphene units, typically involving a Hummers' oxidation step to reduce interactions between graphene layers, leading to the formation of GO. However, excessive oxidation during this process can introduce numerous defects or voids within the GO lattice[25,26], which may weaken its barrier effect in the corrosion resistance applications. Additionally, recovering exfoliated GO from the exfoliation system presents challenges in its redispersion within the resin matrix. Wen et al. reported an in-situ shear exfoliation method for graphite nanoplatelets (GNPs) in a Styrene-Butadiene-Styrene (SBS) matrix. This approach not only prevented the exfoliated GNPs from restacking in the suspension, but also improved their dispersibility in the SBS matrix. The well-dispersed GNPs formed efficient thermally conductive filler networks, reducing the interfacial thermal resistance and exhibiting improved tensile moduli and higher glass transition temperatures[27].
In this contribution, as illustrated in Scheme 1, we propose an in-situ exfoliation of graphite directly within the polymeric matrix, which integrates these steps into a single process. This approach simplifies the fabrication procedure, minimizes graphene aggregation, and improves dispersion uniformity, thereby improving the overall performance of the composite material. We first synthesized a hydroxyethylacrylate (HEA) terminated polybutadiene urethane (HTPU) prepolymer using hydroxyl terminated polybutadiene (HTPB) as the starting material. Subsequently, graphite powder was dispersed in the prepared HTPU prepolymer and stirred at high speed to achieve in-situ exfoliation into graphite nanoplatelets (GN). This GN-containing mixture was directly used to prepare UV-curable composite resins (GN/HTPU). The in-situ exfoliation method eliminates the need for recovery and redispersion of GN, thereby simplifying the preparation process and ensuring excellent dispersion of the nanoplatelets. The UV-cured GN/HTPU composite coatings exhibited good performance in electrochemical corrosion resistance tests, salt spray testing, acid resistance testing, and corrosion resistance in artificial sweat under a direct current electric field.
2. Experimental Section
2.1 Chemicals
Hydroxyl terminated polybutadiene (HTPB, hydroxyl value: 0.65 - 0.70 mmol/g) was purchased from TANYUN Aviation Materials Co. Isobornyl acrylate (IBOA, A.R.), isophorone diisocyanate (IPDI, A.R.) and hydroxyethylacrylate (HEA, A.R.) were purchased from Aladdin Scientific Corp., Shanghai, China. Graphite (C.P.) was received from Sinopharm Chemical Reagent Co. 1-hydroxycyclohexyl acetophenone (184) was used as photoinitiator from Wuxi Meihong Chemical Company, China.
2.2 Preparation of HTPU
HEA-terminated polyurethane (HTPU) was synthesized via a two-step reaction[28]. Initially, 90 g of HTPB was vacuumed at 110 °C for 4 h to remove any residue water. After cooling to room temperature, 100 g of ethyl acetate, 13.6 g of IPDI, a trace amount of 4-methoxyphenol (MEHQ), and an organotin catalyst were added. Then the mixture was stirred mechanically at 45 °C for 1 h. Afterwards, 7.1 g of HEA was added dropwise, and the reaction was continued at 60 °C until the disappearance of NCO group vibrations, as confirmed by IR spectroscopy. Finally, the solvent was removed in a rotary evaporator to obtain the product of HTPU.
2.3 In-situ exfoliation of graphite
0.1 g of graphite powder was dispersed in a mixture of 2 g of HTPU and 20 g of IBOA. Then, a high shear dispersing emulsifier was used to exfoliate graphite to GN under 5,000 rpm for 6 h in an ice bath. The final suspension was referred as GN-IH with a graphite mass concentration of 0.45%.
2.4 Preparation of GN/HTPU UV curable coatings
HTPU, IBOA, GN-IH, and photoinitiator 184 were mixed to prepare UV-curable solutions. The mass composition of the solutions was 30% HTPU, 67% IBOA, and 3% 184. GN-IH was incorporated at mass concentrations of 0.1%, 0.2%, and 0.3%, corresponding to coatings designated as G/HTPU-1, G/HTPU-2, and G/HTPU-3, respectively. The solutions were cast onto substrates using a blade and cured by irradiation with 365 nm LED lamps (160 W) at a distance of 10 cm for 30 seconds.
2.5 Characterizations
Fourier transform infrared (FT-IR) spectra were measured on a Thermo Scientific Nicolet iS50 spectrometer. Scanning electron microscopy (SEM) images were acquired using a Zeiss GeminiSEM 300 field emission scanning electron microscope at an acceleration voltage of 5 kV. Static water contact angles (WCA) were measured with a Dongguan Sindin SDC-100 optical contact angle meter. Raman spectra were acquired on a Renishaw inVia-Reflex Raman spectrometer with a 532 nm laser. Atomic force microscopy (AFM) images were recorded on a Bruker NanoScope® V microscope. Gel permeation chromatography (GPC) with a RI detector (Waters ACQUITY) was employed to determine the molecular weights of HTPB and HTPU, using tetrahydrofuran (THF) as the eluent and narrow molecular weight distribution polystyrene as calibration standards.
2.6 Gel content of the cured coatings
The cured samples with dimensions of 20 mm × 20 mm × 1.2mm were weighed (W i) and immersed in toluene for 2 days at 40 °C and then dried at 120 °C until the weight was constant (W d). The gel content of the samples was calculated by the following Eq. 1[29].
2.7 Mechanical properties
The mechanical properties of the UV samples were evaluated using a universal material testing machine, following the GB/T 2567-2021 standard. The coating solution was poured into a silicone module and irradiated for 90 s. The testing part has dimensions of 100 mm (length) × 50 mm (width) × 43 mm (thickness)[30].
2.8 Electrochemical corrosion testing
Electrochemical polarization measurements were performed on a CHI-604E electrochemical instrument (Chenhua Instruments). A three-electrode setup was employed, consisting of an HTPU-coated Cu sheet as the working electrode, a Pt plate as the counter electrode, and a saturated calomel electrode (SCE) as the reference electrode. The working electrode had an exposed area of 1 cm2 and was immersed in a 3.5 wt% NaCl solution, which served as the electrolyte Prior to measurements, the working electrode was allowed to stabilize for 20 min to establish a stable open circuit potential (OCP). The protective efficiency was calculated according to the following Eq. 2:
Where Icorr(b) and Icorr(c) were self-corrosion current density of bare substrate and coated substrate, respectively[31]. Electrochemical impedance spectroscopy (EIS) measurements were carried out with the frequency range of 10-2 Hz ~ 105 Hz. The EIS data were analyzed using Zview software, with an analytical error of 10%.
2.9 Salt spray testing
A Q235 carbon steel sheet with working area of 12.5 cm2 was used as the substrate. Prior to the test, the sheet was sequentially rinsed with ethanol and acetone to remove the organic residue. Then the UV-curable solutions were applied to the sheets and cured for 30 s. The samples were placed in a salt spray cabinet maintained at a constant temperature of 35 °C, where a 3.5 wt% salt solution was periodically sprayed. The steel sheet was periodically photographed at specific intervals to monitor their condition[32].
2.10 Corrosion behavior of PCB under direct current electric field
A standard testing board (IPC-B 24 with line distance of 2.54 mm) was coated with G/HTPU-2. The thickness was determined to be about 100 μm using a micrometer gauge. The coated board was immersed in a neutral artificial sweat solution and then subjected to DC voltages of 12 V or 24 V for a specified duration. The board was periodically photographed at set intervals to monitor any changes in the coating's appearance and integrity.
3. Results and Discussion
The FTIR spectra of the raw materials and products are shown in Figure 1. The characteristic peaks at 1,640 cm-1 and 967 cm-1 correspond to the trans-olefin structure[33]. The characteristic peak at 2,270 cm-1 corresponds to the stretching vibration of the NCO group of IPDI. In the HEA spectrum, the peaks at 1,640 cm-1 and 810 cm-1 are attributed to the vibrations of C=C. The band at 1,712 cm-1 of HTPU corresponds to the stretching C=O vibration of the carbamate group[34]. The bands at 3,343 and 1,527 cm-1 of HTPU are attributed to the stretching N-H vibration of the carbamate group[34]. The disappearance of the characteristic peak of NCO group at 2,270 cm-1, as well as the appearance of the characteristic peaks of carbamate (3,343 cm-1 and 1,712 cm -1) and the C=C characteristic peaks (1,640 cm-1 and 810 cm -1), indicate the successful synthesis of HTPU.
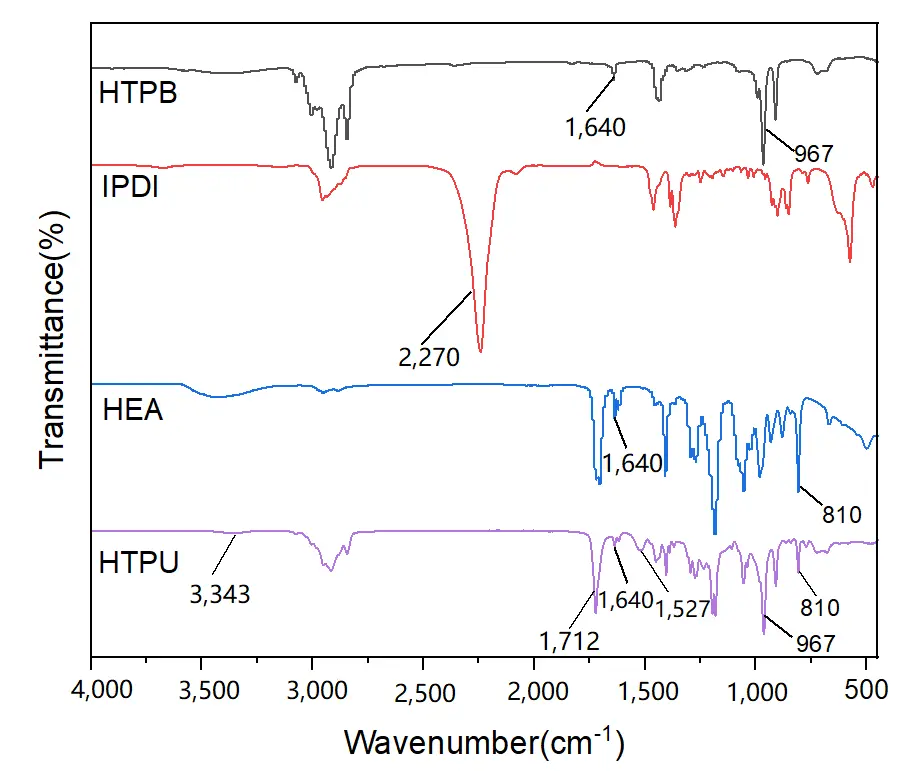
Figure 1. FTIR spectra of the starting reagents and the prepared prepolymer HTPU. FTIR: Fourier transform infrared spectroscopy; HTPU: hydroxyethylacrylate terminated polybutadiene urethane.
HTPB and the prepolymer HTPU were dissolved in anhydrous THF. As shown in Figure S1, the GPC profile of HTPU shifts to a higher molecular weight region compared to that of HTPB. The calibrated values of Mn and Mw for HTPB are 5,503 and 9,946 g/mol, respectively. After the reaction, the values of Mn and Mw for HTPU increase to 11,745 and 20,794 g/mol, respectively, while the polydispersity remains around 1.8. The molecular weights of HTPU are nearly double those of HTPB, indicating that HTPB chains are connected through IPDI during the reaction.
SEM image (Figure 2a) shows that the graphite particles are composed of sheets arranged in overlapping layers of varying thicknesses. After shear exfoliation in the HTPU/IBOA solution, GN are clearly observed in Figure 2b. AFM image confirms that these GN consist of several layers of graphene stacked together (Figure 2c). The height profile in Figure 2d indicates that the thin regions of GN are approximately 7 nm thick, while the thicker regions are about 12 nm thick. Given the theoretical thickness of a single graphene layer (0.34 nm), this suggests that the GN comprises around 20 to 35 layers of graphene. The Raman spectra (Figure 3) exhibit two prominent peaks at ~ 1,351 cm-1 and ~ 1,581 cm-1, corresponding to the D band and G band of graphite, respectively. After exfoliation, the intensity ratio ID/IG increases from 0.15 to 0.35, indicating that the conjugated structure of graphite is exfoliated to loosen graphite nanoplatelets.
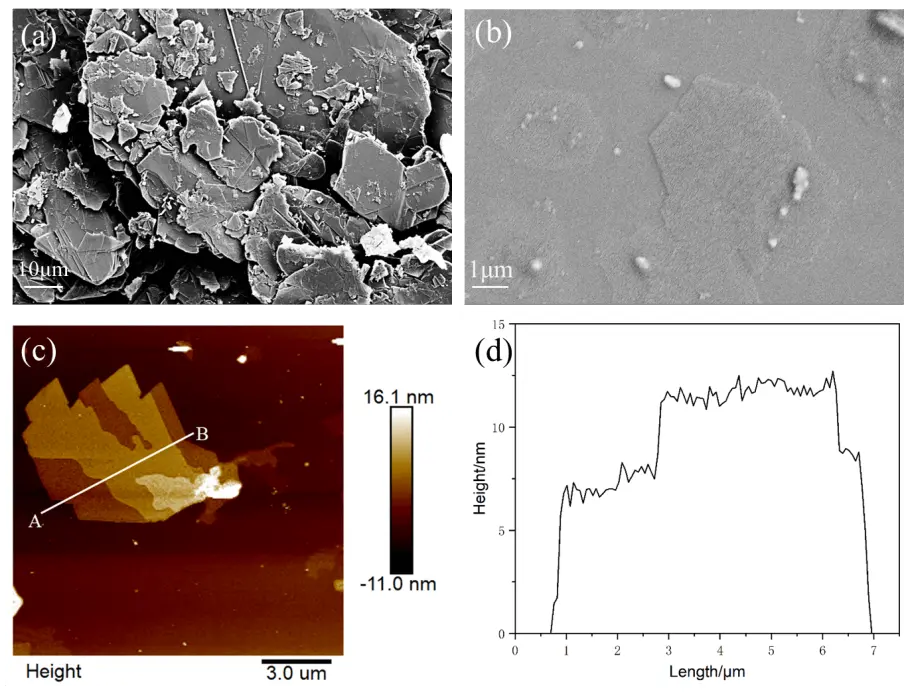
Figure 2. SEM images of graphite powder (a) and exfoliated GN (b); AFM images of the exfoliated GN (c) and the corresponding height profile of the exfoliated GN (d). SEM: scanning electron microscopy; GN: graphite nanoplatelets; AFM: atomic force microscopy.
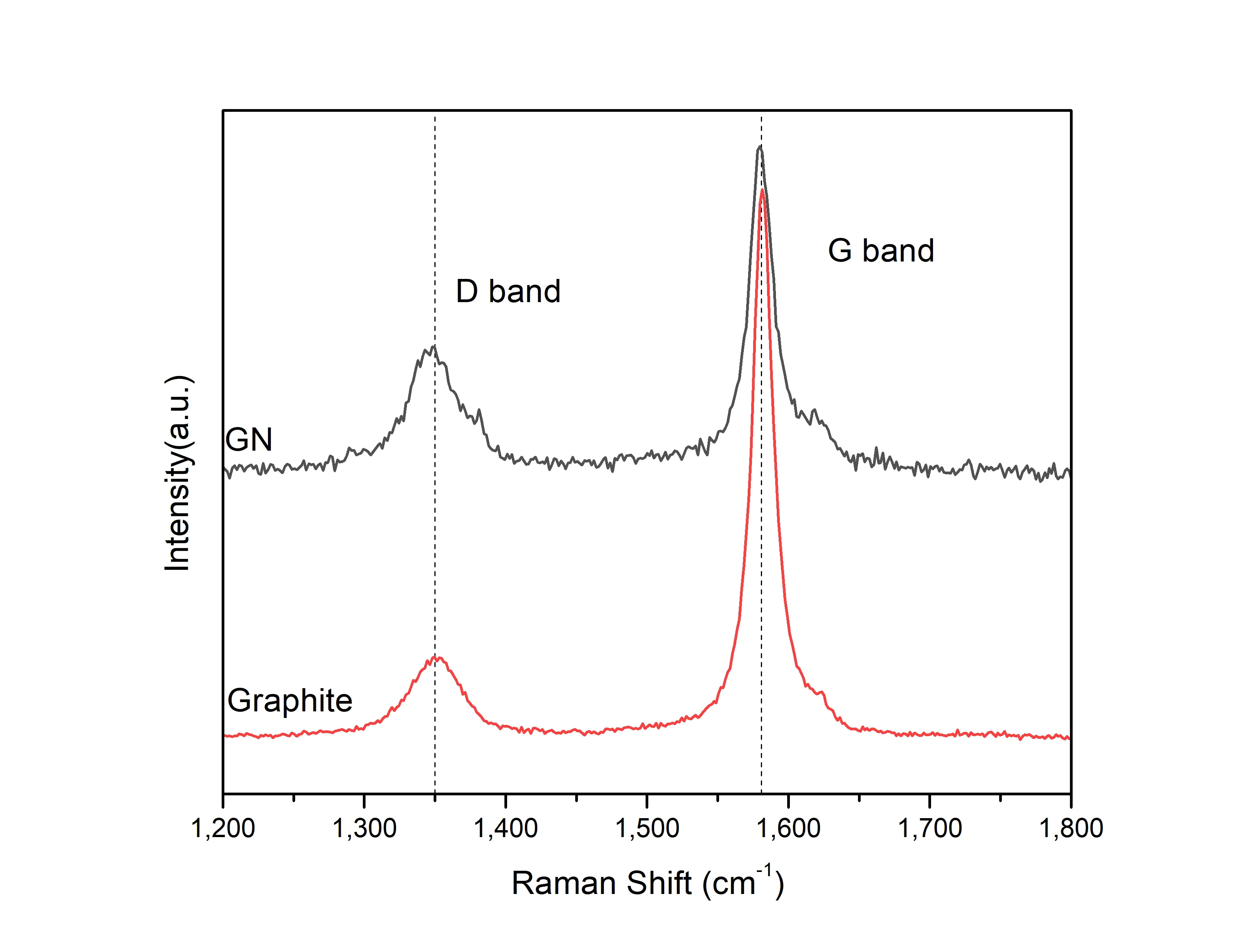
Figure 3. Raman spectra of graphite and the exfoliated GN. GN: graphite nanoplatelets.
It has been demonstrated that high-speed shear in a liquid medium can generate sufficient energy to overcome the interactions between graphene layers and thus delaminate graphite flakes[26,35]. In this contribution, shear force originating from the viscous HTPU/IBOA solution delaminates graphite into smaller GN. In addition, HTPU macromolecules adsorb onto the GN surface through π-π interactions, preventing GN coalescence. The GN-containing HTPU/IBOA solution (GN-IH) is directly used to prepare UV-curable coating solutions. The preparation method eliminates the steps of recovery, drying and redispersion typically required in the conventional process of incorporating graphene. As shown in Figure 4a, GNs are well dispersed in the HTPU to form dark coating solutions. The color becomes darker when increasing the GN content. No sedimentation of GN at the bottom is observed even after settling for three days. UV coatings with various GN contents are prepared on a glass substrate to obtain uniform films with a thickness of approximately 6 μm (Figure 4b,c,d,e). The water contact angle (WCA) of the coatings increases as the GN content increases, ranging from 92 for HTPU to 106 for G/HTPU-3 (Figure 4f). The incorporation of GN increases the hydrophobicity of the HTPU coatings. A clean graphene surface may present hydrophilic nature due to H–π interactions with water molecules. However, surface contamination, e.g. nanoparticles, can weaken the interactions. Water molecules form a Cassie-Baxter wetting state on the contaminated graphene, resulting in the hydrophobic nature of the exfoliated graphite nanoplatelets[36]. Consequently, the hydrophobicity of the HTPU coating increases with the addition of more graphite nanoplatelets.
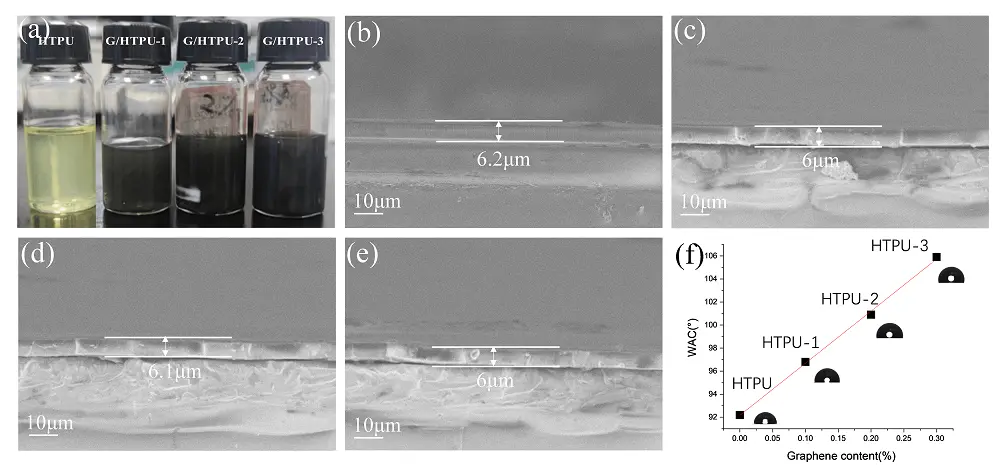
Figure 4. Photographs of HTPU and G/HTPU coating solutions (a); cross-sectional SEM images of HTPU (b); G/HTPU-1 (c); G/HTPU-2 (d) and G/HTPU-3 (e); water contact angles of coatings (f). HTPU: hydroxyethylacrylate terminated polybutadiene urethane; SEM: scanning electron microscopy.
The conversion of the UV curable coatings is assessed by the gel content after UV radiation. The gel content of HTPU, G/HTPU-1, G/HTPU-2 and G/HTPU-3 is 95.2%, 94.5%, 94.3%, and 94.1%, respectively, indicating high conversion after curing. An increase in GN content results in a slight decrease in gel content. The mechanical properties of the UV coatings are presented in Table 1. Elongation at break decreases from 17.58% to 11.64% as GN content increases. The incorporation of GN, which has a rigid structure, decreases the elongation of the UV coatings. On the other hand, the elastic modulus significantly improves from 66.42 MPa to 163.41 MPa, and tensile strength at break enhances from 28.8 MPa to 29.5 MPa when increasing GN content. Nevertheless, further increases in GN content lead to a decrease in both elastic modulus and tensile strength. The possible reason is that an excess of GN hinders the curing of the coating solution, thereby decreasing the mechanical properties.
Samples | Elastic modulus (MPa) | Elongation at break (%) | Tensile strength (MPa) |
HTPU | 66.42 | 17.58 | 28.8 |
G/HTPU-1 | 88.06 | 16.30 | 29.2 |
G/HTPU-2 | 163.41 | 12.42 | 29.5 |
G/HTPU-3 | 122.86 | 11.64 | 29.4 |
HTPU: hydroxyethylacrylate terminated polybutadiene urethane; UV: ultraviolet.
Tafel polarization testing is a conventional method to evaluate the corrosion resistance of coatings. The lower and further to the right the Tafel curves shift, the better the coating resists corrosion. As shown in Figure 5a, the Tafel curve of the HTPU coated Cu sheet evidently shifts to a lower current density and more positive potential compared to that of the bare Cu sheet. The HTPU coating efficiently prevents corrosion of metal substrate from the corrosion medium. Compared to HTPU, the Tafel curves of the GN-incorporated HTPU coatings shift even further to the lower right, indicating superior corrosion resistance for GN/HTPU coatings. Corrosion data derived from the Tafel curves are collected in Table 2. The corrosion current densities (I corr) of GN/HTPU-1, GN/HTPU-2 and GN/HTPU-3 coatings are remarkably reduced to 1.84 × 10-8, 1.03 × 10-8 and 1.36 × 10-8 A·cm-2, respectively, which are much lower than that of HTPU (38.7 × 10-8 A·cm -2). All G/HTPU coatings exhibit a maximum corrosion rate lower than 2.13 × 10-4 mm·year−1, which is significantly slower than that of HTPU coating. The Tafel curves for the G/HTPU coated Cu sheet yield an Ecorr higher than -206 mV, which is more positive than for the bare Cu sheet and HTPU at -287 and -245 mV, respectively. Among the coatings with different GN contents, G/HTPU-2 demonstrates the best corrosion protection performance.
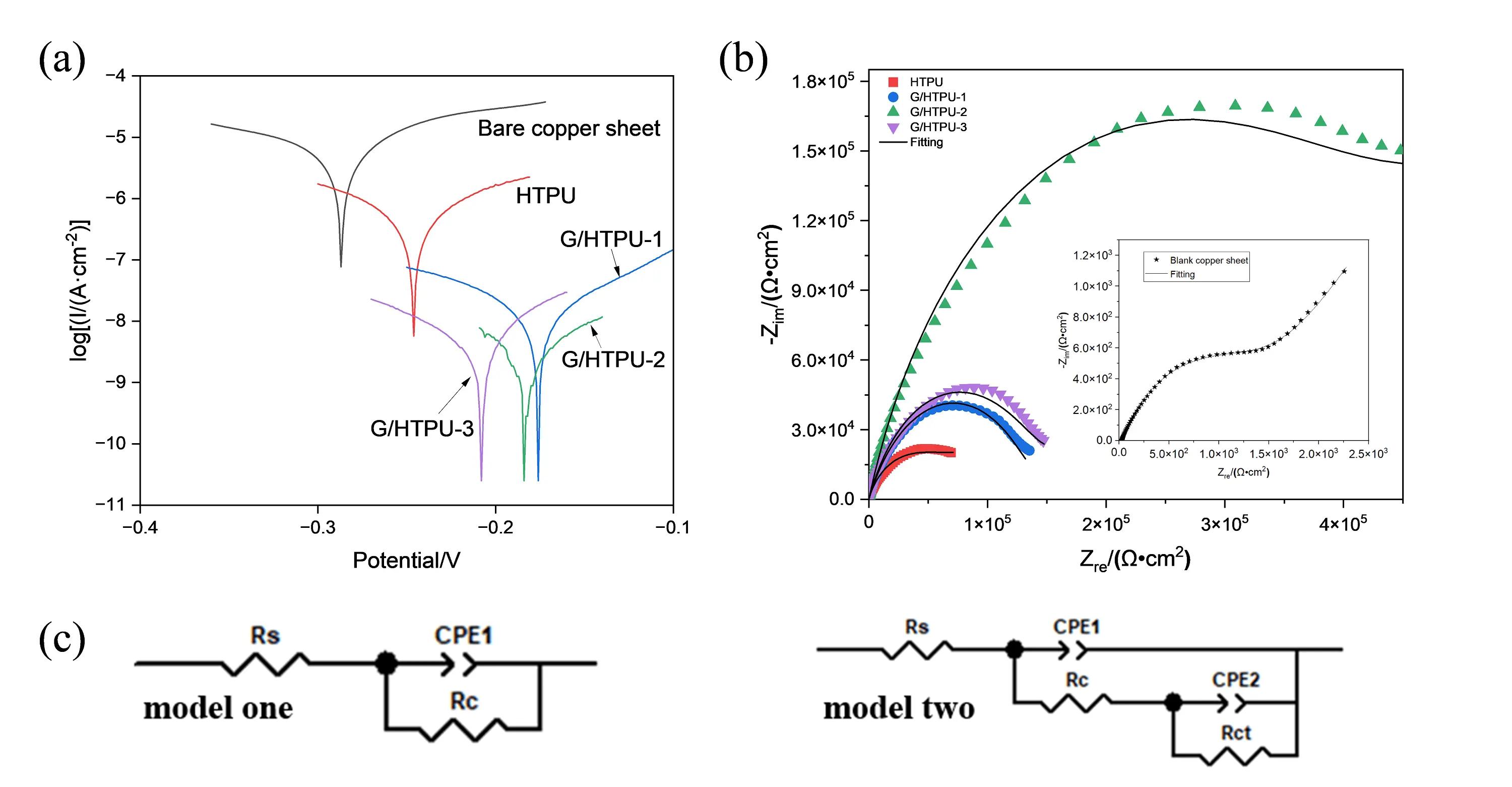
Figure 5. Tafel polarization curves (a); Nyquist plots (b) of HTPU and G/HTPU coated on Cu substrate, and the equivalent circuits used for fitting the Nyquist plots. HTPU: hydroxyethylacrylate terminated polybutadiene urethane.
sample | I corr/(10-8 A·cm -2) | Ecorr/mV | R/10-4 (mm·a -1) | Pe/% |
Bare Cu substrate | 1,548 | -287 | — | — |
HTPU | 38.7 | -245 | 44.81 | 97.66% |
G/HTPU-1 | 1.84 | -176 | 2.13 | 99.89% |
G/HTPU-2 | 1.03 | -183 | 1.19 | 99.94% |
G/HTPU-3 | 1.36 | -206 | 1.57 | 99.92% |
Icorr: self-corrosion current; Ecorr: self-corrosion potential; R: corrosion rate; HTPU: hydroxyethylacrylate terminated polybutadiene urethane.
The electrochemistry corrosion behavior of the coatings is further investigated by analyzing the EIS data. The capacitance arc radius of the G/HTPU coatings is apparently larger than that of the HTPU coatings. Among the G/HTPU coatings, the G/HTPU-2 coating exhibits the largest capacitance arc radius, indicating the best corrosion resistance performance (Figure 5b). Equivalent circuit model 1 and model 2 have been used to fit the bare and G/HTPU coated Cu sheets, respectively (Figure 5c). Here, Rs is the solution resistance, Rc corresponds to the penetrating resistance of the coating, Rct is the charge transfer resistance. CPE1 and CPE2 are the constant phase elements representing the single-layer and double-layer capacitive response of the coatings, respectively. The EIS data are well-fitted by the models. The Rc value increases from 1.160 × 103 Ω·cm2 to 5.082 × 103 Ω·cm2 after the Cu sheet is coated with HTPU. Additionally, the Rc value exceeds 1.400 × 105 Ω·cm2 for the G/HTPU coatings, reaching 4.349 × 105 Ω·cm2 for G/HTPU-2. GN have high aspect ratios, which can delay the diffusion of corrosion media through the labyrinth effect, greatly improving the corrosion resistance of metals[37,38]. However, when the GN content is further increased, the anti-corrosion performance of the coating decreases, likely because excess GN could not be well dispersed in the coatings. The agglomeration of GN in the coatings leads to the formation of breakthrough paths, resulting in a decrease in the anti-corrosion performance.
Salt spray testing is used to simulate accelerated chemical corrosion of metals in natural environments. The UV-curable coating solutions were cast onto Q235 carbon steel sheets to get coatings with a thickness of approximately 50 μm. As shown in Figure 6, the bare Q235 carbon steel sheet exhibits severe corrosion after only 24 hours of testing. By contrast, the HTPU-coated sample shows little corrosion. In addition, the corrosion is further inhibited by the G/HTPU coatings. Notably, for the G/HTPU-2 coated sample, no corrosion is observed even after 72 hours of testing (Figure S2). The results of the salt spray testing in a gaseous corrosive medium coincide well with those of the electrochemical corrosion test in a liquid corrosive medium, indicating that the GN-incorporated HTPU UV-cured coatings provide effective corrosion protection.
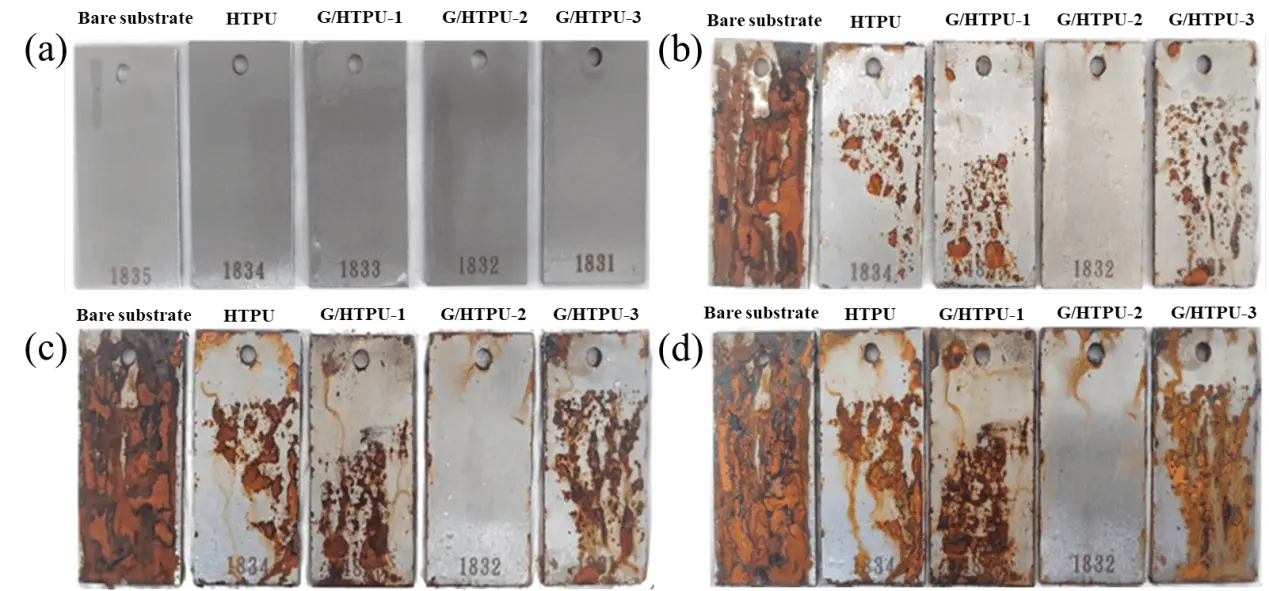
Figure 6. Photographs of the samples after the salt spray testing for different intervals: (a) 0 h; (b) 24 h; (c) 48 h; (d) 72 h.
The acid resistance performance of the G/HTPU-2 coating was also evaluated using a galvanized sheet as the substrate. The upper half of the sheet was coated with G/HTPU-2 to a thickness of 100 μm. Selected areas of the coated upper half and the bare lower half are sealed contacting 0.5 mol/L H2SO4 solution (Figure 7a). After 24h of testing at r.t., the selected area of the bare lower half developed a dark spot due to acid corrosion. On the other hand, no signs of corrosion are observed on the coated upper half, indicating that the G/HTPU-2 coating efficiently protects the metal substrate from acid corrosion (Figure 7b).
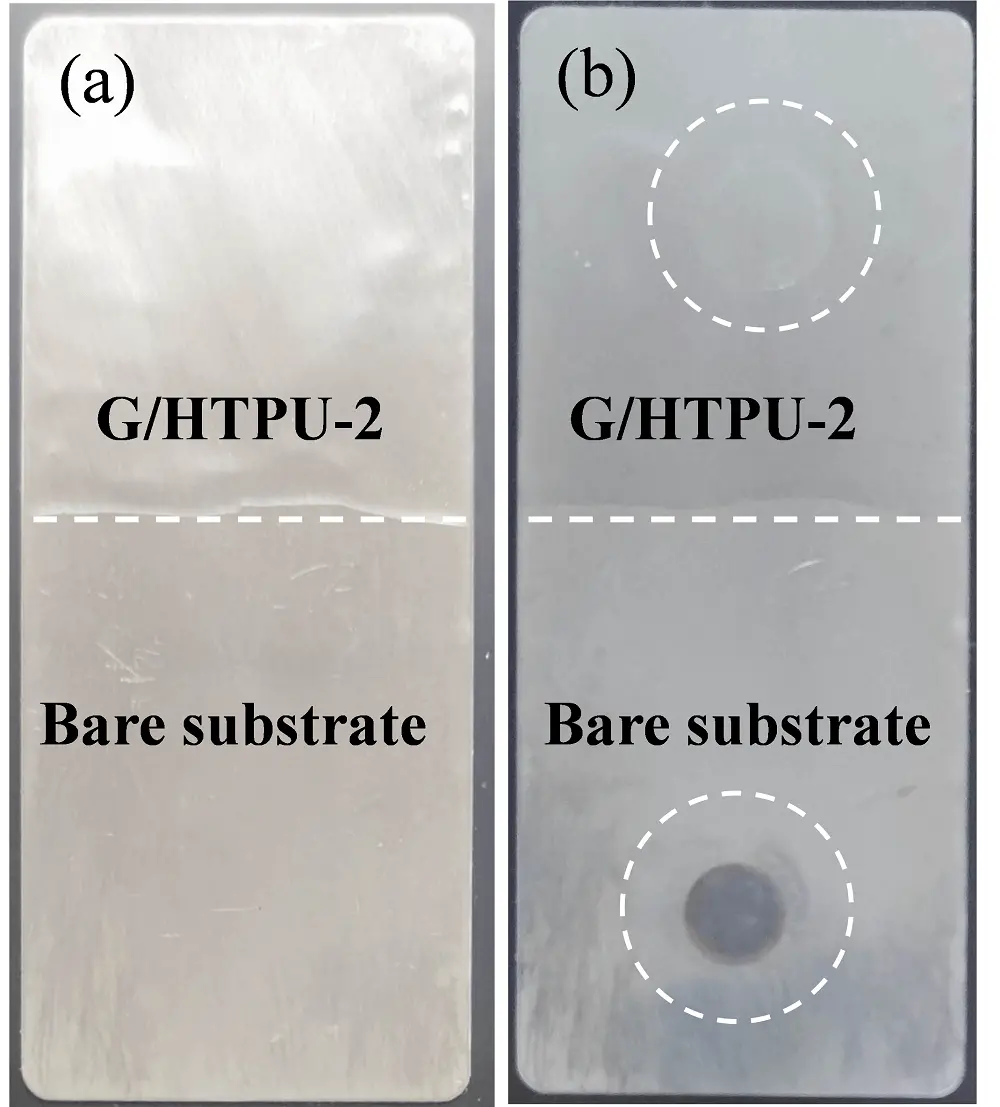
Figure 7. Comparative photographs of the bare and G/HTPU-2 coated galvanized sheet before (a) and after (b) 24 h of 0.5 mol/l H2SO4 acid contacting. HTPU: hydroxyethylacrylate terminated polybutadiene urethane.
To ensure that the G/HTPU-2 coating offers effective protection for powered circuit boards, we conducted specialized tests to evaluate its performance (Figure 8a,b). As shown in Figure 8c,d,e,f, when the G/HTPU-2-coated standard test printed circuit board (PCB) IPC-B-24 was immersed in neutral artificial sweat for 72 hours under a 12 V power supply, no corrosion was observed. This demonstrates that the G/HTPU-2 coating can effectively protect the board for more than 72 hours in neutral artificial sweat under 12 V power. Additionally, as illustrated in Figure 8e,f, after a 72-hour test at 12 V, the coating remained intact even when subjected to an additional 48 hours under a 24 V direct current field. This confirms that the coating can continue to offer effective protection for more than 48 hours under 24 V power. The G/HTPU-2 coating exhibits outstanding protective capabilities for the PCBs in neutral artificial sweat under powered conditions. By contrast, severe corrosion occurs after testing at 12 V for 24 h for HTPU and G/HTPU-1 (Figure S3). Platelike materials, e.g. GN used in this work, possess high aspect ratios. The well dispersed GNs in the HTPU coatings delay the diffusion of corrosive media through the labyrinth effect. As a result, the incorporation of GN greatly improve the corrosion and acid resistance of the coatings.
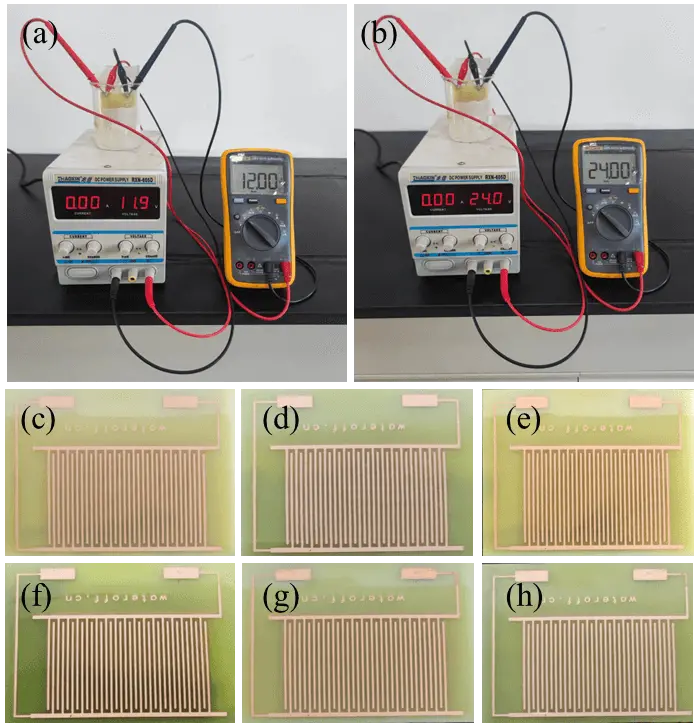
Figure 8. Photographs of testing devices (a, b) and G/HTPU-2 coated IPC board after testing for different intervals (c) 0 h; (d) 12 V, 24 h; (e) 12 V, 48 h; (f) 12 V, 72 h; (g) 12 V, 72 h and 24 V, 24 h; (h) 12 V, 72 h and 24 V, 48 h. IPC: International Printed Circuit.
4. Conclusion
An in-situ mechanical exfoliation of graphite was achieved through high-speed shearing in a mixture of hydroxyethylacrylate terminated polybutadiene urethane (HTPU) prepolymer and reactive diluent. The as-obtained GN, with a thickness of 7 ~ 12 nm, consist of approximately 20 ~ 35 layers of graphene. GN-incorporated HTPU (GN/HTPU) coating solutions were successfully prepared by directly mixing the GN-containing mixture with prepolymer, reactive diluent, and photoinitiator. The incorporation of GN significantly enhances the corrosion resistance of the coating due to the labyrinth effect. Specifically, the G/HTPU-2 composite coating, with a GN content of 0.2%, demonstrates the best corrosion resistance in both electrochemical polarization and salt spray tests. A G/HTPU-2-coated standard test PCB successfully survives immersion in neutral artificial sweat under a direct current field of 12 V for 72 h, followed by 24 V for an additional 48 h. The GN/HTPU UV-curable coatings show promising potential for applications in protecting electronic devices.
Supplementary materials
The supplementary material for this article is available at: Supplementary materials.
Authors contribution
Shen Z: Performed the experiments, wrote the original manuscript.
An M, Li S: Performed the experiments.
Mi X: Conceived the experiments.
Xiao Q: Designed the experiments, wrote and revised the paper.
All authors approved the final version of the manuscript.
Conflicts of interest
This research received financial support from the Beijing Thinvec Conjoint Project. No other conflicts of interest to declare.
Ethical approval
Not applicable.
Consent to participate
Not applicable.
Consent for publication
Not applicable.
Availability of data and materials
The data and materials could be obtained from the corresponding author upon request.
Funding
This study was supported by the National Natural Science Foundation of China (Grant No. 22075253) and Beijing Thinvec Co. Ltd.
Copyright
© The Author(s) 2025.
References
-
1. Hu Q, Liu C, Liang X, Mi X, Zhou Q, Zhu W, et al. Boron nitride/fluorinated polyacrylate composite material coatings with high corrosion resistance. J Zhejiang Norm Univ. 2022;45(04):411-418. Chinese.
[DOI] -
2. Huong DQ, Duong T, Nma PC. Experimental and theoretical study of corrosion inhibition performance of N-phenylthiourea for mild steel in hydrochloric acid and sodium chloride solution. J Mol Model. 2019;25(7):204.
[DOI] -
3. Angst UM. A Critical review of the science and engineering of cathodic protection of steel in soil and concrete. Corrosion. 2019;75(12):1420-1433.
[DOI] -
4. Bamdad H, Hawboldt K, MacQuarrie S. A review on common adsorbents for acid gases removal: Focus on biochar. Renew Sust Energ Rev. 2018;81:1705-1720.
[DOI] -
5. Helm C, Raupach M. Development of a numerical simulation model considering the voltage drops within CP anode systems in RC structures. Mater Corros. 2016;67(6):621-630.
[DOI] -
6. Lv A, Sun J, Hu Q, Mi X, Xiao Q. Preparation of EDOT-fluoropolymer coatings and their anti-corrosion properties. J Zhejiang Norm Univ. 2023;46(04):408-415. Chinese.
[DOI] -
7. Huang S, Fang Z, Chen D, Yu Z, Sun Z, Zhang Y. Fabrication of mechanochemically robust superhydrophobic coating based on MPVDF/epoxy resins composites. Prog Org Coat. 2022;163:106651.
[DOI] -
8. Das A, Mahanwar P. A brief discussion on advances in polyurethane applications. Adv Ind Eng Polym Res. 2020;3(3):93-101.
[DOI] -
9. Hithesh MC, Mohana KNS, Harsha YM, Sreelakshmi M, Madhusudhana AM, Kumar MCS. Effects of curing temperature and addition of functionalized graphene oxide on corrosion barrier performance of phenol furfural polymer-amino phenolic resin composite. Prog Org Coat. 2024;188:108164.
[DOI] -
10. Honda K, Morita M, Otsuka H, Takahara A. Molecular aggregation structure and surface properties of poly(fluoroalkyl acrylate) thin films. Macromolecules. 2005;38(13):5699-5705.
[DOI] -
11. Xing W, Jie G, Song L, Wang X, Lv X, Hu Y. Flame retardancy and thermal properties of epoxy acrylate resin/alpha-zirconium phosphate nanocomposites used for UV-curing flame retardant films. Mater Chem Phys. 2011;125(1-2):196-201.
[DOI] -
12. Park YJ, Lim DH, Kim HJ, Park DS, Sung IK. UV- and thermal-curing behaviors of dual-curable adhesives based on epoxy acrylate oligomers. Int J Adhes Adhes. 2009;29(7):710-717.
[DOI] -
13. Liang H, Ding J, Shi W. Kinetics and mechanism of thermal oxidative degradation of UV cured epoxy acrylate/phosphate triacrylate blends. Polym Degrad Stabil. 2004;86(2):217-223.
[DOI] -
14. Li Z, Shen X, Ran C. Synthesis of alkali-soluble resin and its application in UV curable solder resist ink. Chem Ind Eng Prog. 2010;29(04):753-766. Chinese.
[DOI] -
15. Li P, Fan L, Shen W, Wang F. Corrosion protection performance of stretched graphene-modified cold-sprayed zinc coating for steel rebar. Structures. 2024;68:107173.
[DOI] -
16. Nadeem A, Maqsood MF, Raza MA, Karim MR, Ghafoor F, Lee Y, et al. Thermally stable and anti-corrosive polydimethyl siloxane composite coatings based on nanoforms of boron nitride. Inorg Chem Commun. 2024;168:112989.
[DOI] -
17. Kalendova A, Sapurina I, Stejskal J, Veselý D. Anticorrosion properties of polyaniline-coated pigments in organic coatings. Corros Sci. 2008;50(12):3549-3560.
[DOI] -
18. Mo M, Zhao W, Chen Z, Yu Q, Zeng Z, Wu X, et al. Excellent tribological and anti-corrosion performance of polyurethane composite coatings reinforced with functionalized graphene and graphene oxide nanosheets. RSC Advances. 2015;5(70):56486-56497.
[DOI] -
19. Liu D, Zhao W, Liu S, Cen Q, Xue Q. Comparative tribological and corrosion resistance properties of epoxy composite coatings reinforced with functionalized fullerene C60 and graphene. Surf Coat Tech. 2016;286:354-364.
[DOI] -
20. Liu C, Hu Q, Liang X, Mi X, Zhou Q, Zhu W, et al. On preparation and corrosion resistance test for graphene/fluorinated polyacrylate polymer composite coatings. J Zhejiang Norm Univ. 2021;44(03):278-285. Chinese.
[DOI] -
21. Dadkhah S, Gharieh A. UV-cured acrylated PANI/graphene oxide nanocomposite coating with superior anticorrosive protection and self-healing abilities. Prog Org Coat. 2024;189:108346.
[DOI] -
22. Dadkhah S, Gharieh A, Khosravi M. Eco-friendly UV-curable graphene oxide/fluorinated polyurethane acrylate nanocomposite coating with outstanding anticorrosive performance. Prog Org Coat. 2024;186:108020.
[DOI] -
23. Jafarifard S, Ebrahimi M, Sharif F. Antistatic epoxy acrylate/graphene oxide UV-curable coatings with improved shrinkage and adhesion strength. Prog Org Coat. 2023;182:107595.
[DOI] -
24. Ma Y, Ye Y, Wan H, Chen L, Zhou H, Chen J. Chemical modification of graphene oxide to reinforce the corrosion protection performance of UV-curable polyurethane acrylate coating. Prog Org Coat. 2020;141:105547.
[DOI] -
25. Shen X, Wang Z, Wu Y, Liu X, Kim JK. Effect of functionalization on thermal conductivities of graphene/epoxy composites. Carbon. 2016;108:412-422.
[DOI] -
26. Shen B, Zhai W, Chen C, Lu D, Wang J, Zheng W. Melt blending iIn situ enhances the interaction between polystyrene and graphene through π-π stacking. ACS Appl Mater Interfaces. 2011;3(8):3103-3109.
[DOI] -
27. Wen Y, Xue Y, Li X, Pei H, Zhou H, Feng Y, et al. In-situ shear exfoliation and thermal conductivity of SBS/Graphite nanoplatelet nanocomposites. Compos Part B Eng. 2020;197:108172.
[DOI] -
28. Xia W, Zhu N, Hou R, Zhang W, Chen M. Preparation and characterization of fluorinated hydrophobic UV-crosslinkable thiol-ene polyurethane coatings. Coatings. 2017;7(8):117.
[DOI] -
29. Hwang HD, Kim HJ. Enhanced thermal and surface properties of waterborne UV-curable polycarbonate-based polyurethane (meth)acrylate dispersion by incorporation of polydimethylsiloxane. React Funct Polym. 2011;71(6):655-665.
[DOI] -
30. Dolci E, Michaud G, Simon F, Boutevin B, Fouquayc S, Caillol S. Remendable thermosetting polymers for isocyanate-free adhesives: a preliminary study. Polym Chem. 2015;6(45):7851-7861.
[DOI] -
31. Zhang H, Zhai H. Study on the use of corrosion coupons to control atmospheric corrosion salt spray tests. Shanghai Coat. 2017;55(02):43-48. Chinese. Available from: https://kns.cnki.net/kcms2/article/abstract
-
32. Liang X, Liu C, Mi X, Zhu W, Zhou Q, Xiao Q. Preparation and corrosion resistance of SiO2 or TiO2 nano particles/fluorinatedpolyacrylate polymer composite coatings. Acta Mater Compo. Sin. 2020;37(8):1832-1840.
[DOI] -
33. Ma L, Zhu X, Zhang W, Zhang H, Wang J, Qu J. Study on the preparation and performance comparison of side-chain hydroxyl-terminated polybutadiene derivatives with narrowly molecular weight distribution used for polyurethane. Polym Test. 2021;104:107389.
[DOI] -
34. Malkappa K, Jana T. Simultaneous improvement of tensile strength and elongation: An unprecedented observation in the case of hydroxyl terminated polybutadiene polyurethanes. Ind Eng Chem Res. 2013;52(36):12887-12896.
[DOI] -
35. Liu L, Shen Z, Yi M, Zhang X, Ma S. A green, rapid and size-controlled production of high-quality graphene sheets by hydrodynamic forces. RSC Adv. 2014;4(69):36464-36470.
[DOI] -
36. Zhang J, Jia K, Huang Y. Intrinsic wettability in pristine graphene. Adv Mater. 2022;34:2103620.
[DOI] -
37. Gu L, Ding J, Yu H. Research in graphene-based anticorrosion coatings. Prog Chem. 2016;28(5):737-743.
[DOI] -
38. Lu H, Zhang S, Zhao Z, Zhou Y, Li W. Preparation and corrosion protection of VB2 modified trimer aniline-reduced graphene oxide(VTA-rGO) coatings. Prog Org Coat. 2019;132:95-99.
[DOI]
Copyright
© The Author(s) 2025. This is an Open Access article licensed under a Creative Commons Attribution 4.0 International License (https://creativecommons.org/licenses/by/4.0/), which permits unrestricted use, sharing, adaptation, distribution and reproduction in any medium or format, for any purpose, even commercially, as long as you give appropriate credit to the original author(s) and the source, provide a link to the Creative Commons license, and indicate if changes were made.
Publisher's Note
Share And Cite